How Steel Castings are Made
Steel castings are produced from recycled scrap steel melted in an Electric Arc Furnace (EAF) or Induction Furnace.
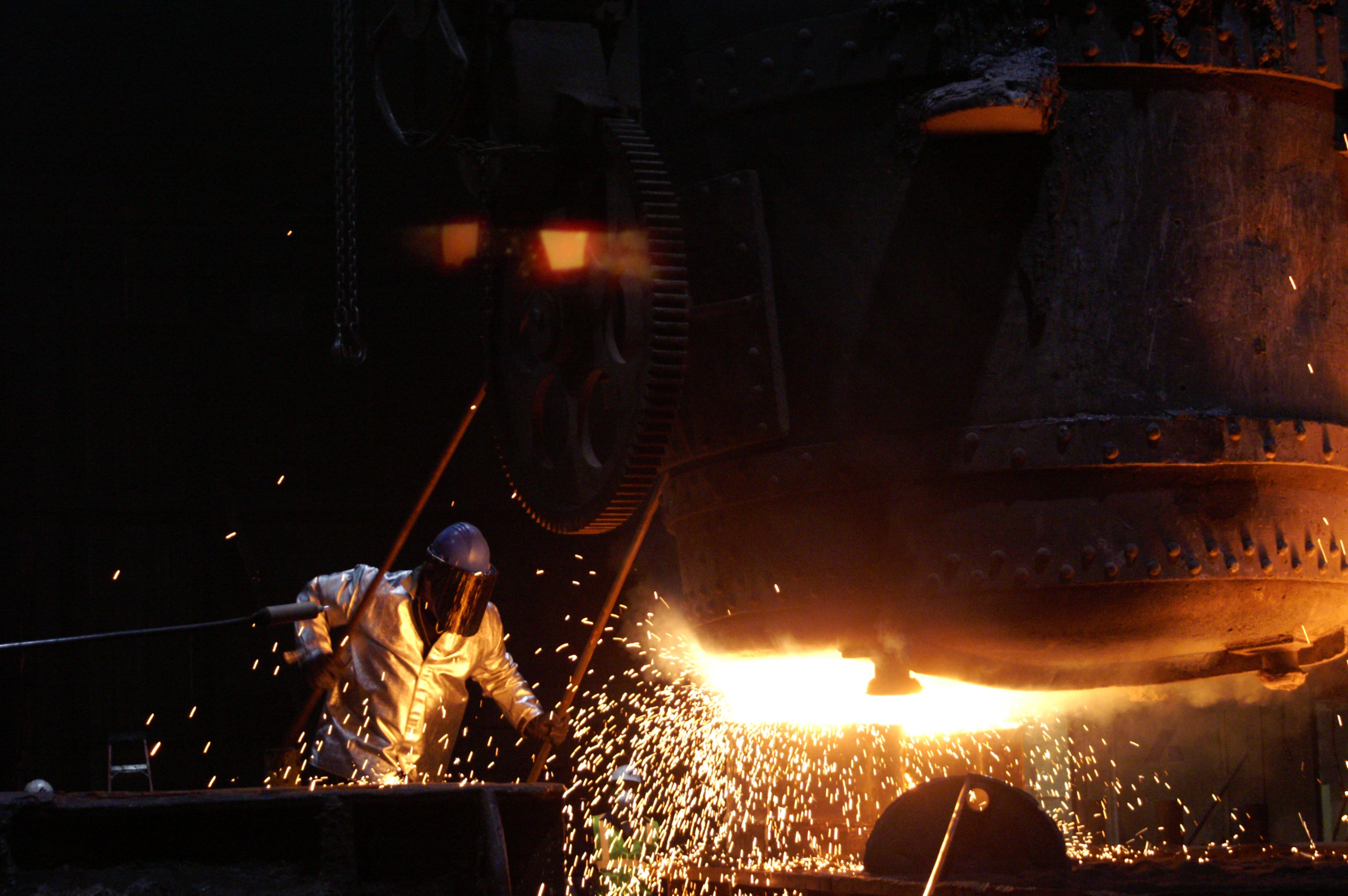
DESIGN
CAST CONNEX designs are responsive to the structural and architectural needs of the project as well as to the constraints of the casting manufacturing process
A casting design first moves from the digital to the physical realm during patternmaking.
3D digital models developed during the design process are used to create patterns – a replica of the part to be cast – which are used in the mold making process. Patterns are typically made from wood, resin, or aluminum and are produced via CNC-manufacturing. Additive manufacturing (3D printing) can also be used in patternmaking.
Molding
Patterns are used multiple times to generate sand molds for each unique casting geometry
Pouring
The Transition From Molten
to Cast Steel
Heat Treatment
Steel castings exhibit isotropic mechanical properties
In steel casting manufacturing, heat treatment is employed in conjunction
with alloying to achieve the desired mechanical properties in the casting. Heat treatment also relieves residual stresses that may have developed during solidification or casting production welding.
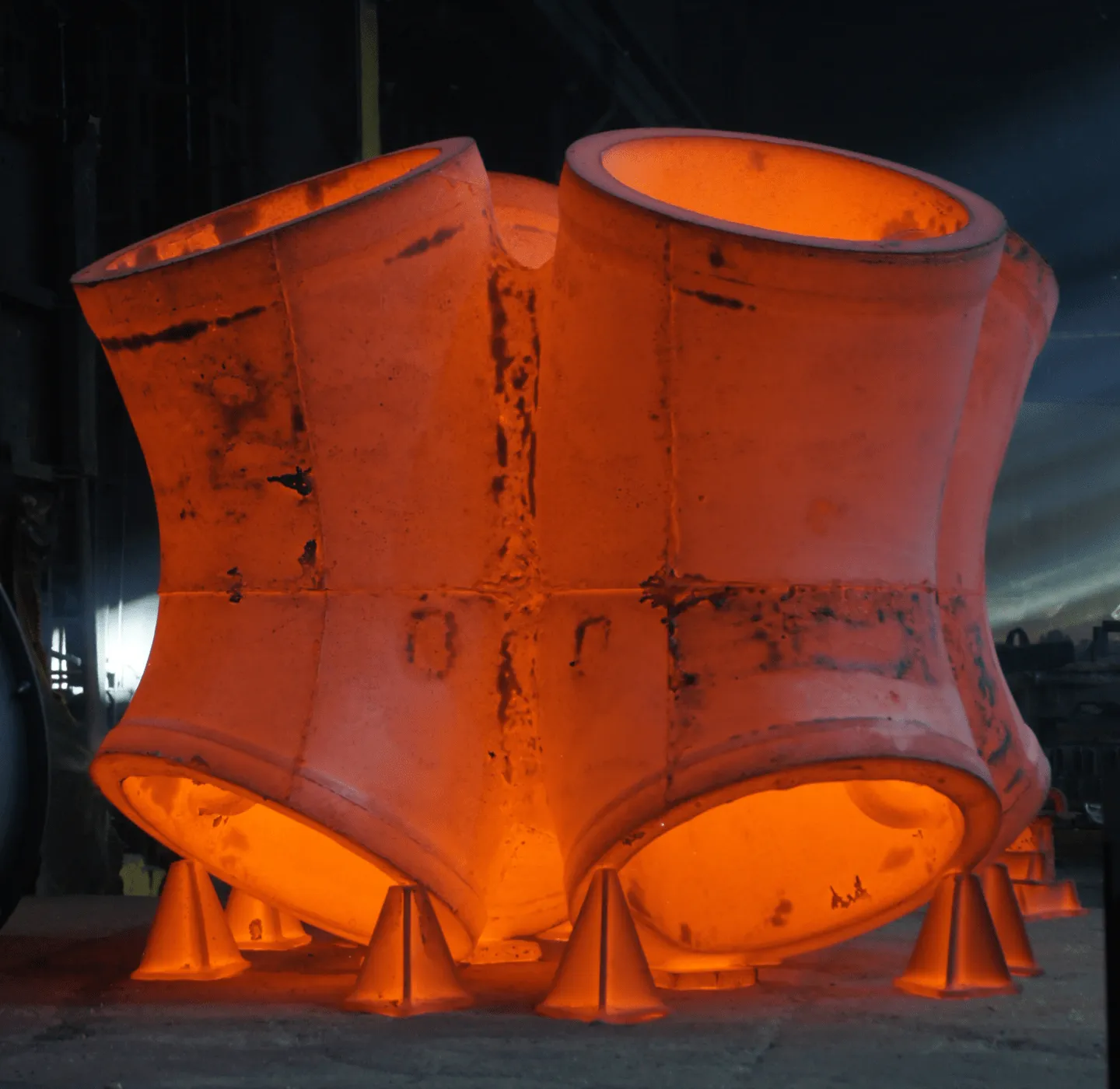
Ensuring Steel Castings Meet Performance Requirements
Tensile and Charpy (CVN) impact testing is typically conducted on cast steel material that is cast from the same heat as, and heat treated along with, the component that it is intended to represent. This may take the form of test blocks, alternatively, coupons can be cut directly from castings (or the parts of castings) that have been set aside for destructive testing.
Yield strength, tensile strength, elongation, reduction of area, and CVN toughness are measured for each heat and reported on Certified Material Test Reports (CMTRs) provided for every CAST CONNEX product.
Featured Projects
Harness the Power of Steel Castings in Your Projects
Contact Us
Want to leverage steel castings in your work?
Whether your interest in cast steel components is general or project-specific, we look forward to speaking with you.