PROJECT BRIEF
The first major project under the University of Victoria new Campus Plan is open: the award-winning Student Dining and Housing project designed by Perkins&Will and Fast + Epp. This mixed-use facility boosts bed, dining, academic and common spaces while achieving LEED v4 Gold and Passive House targets.
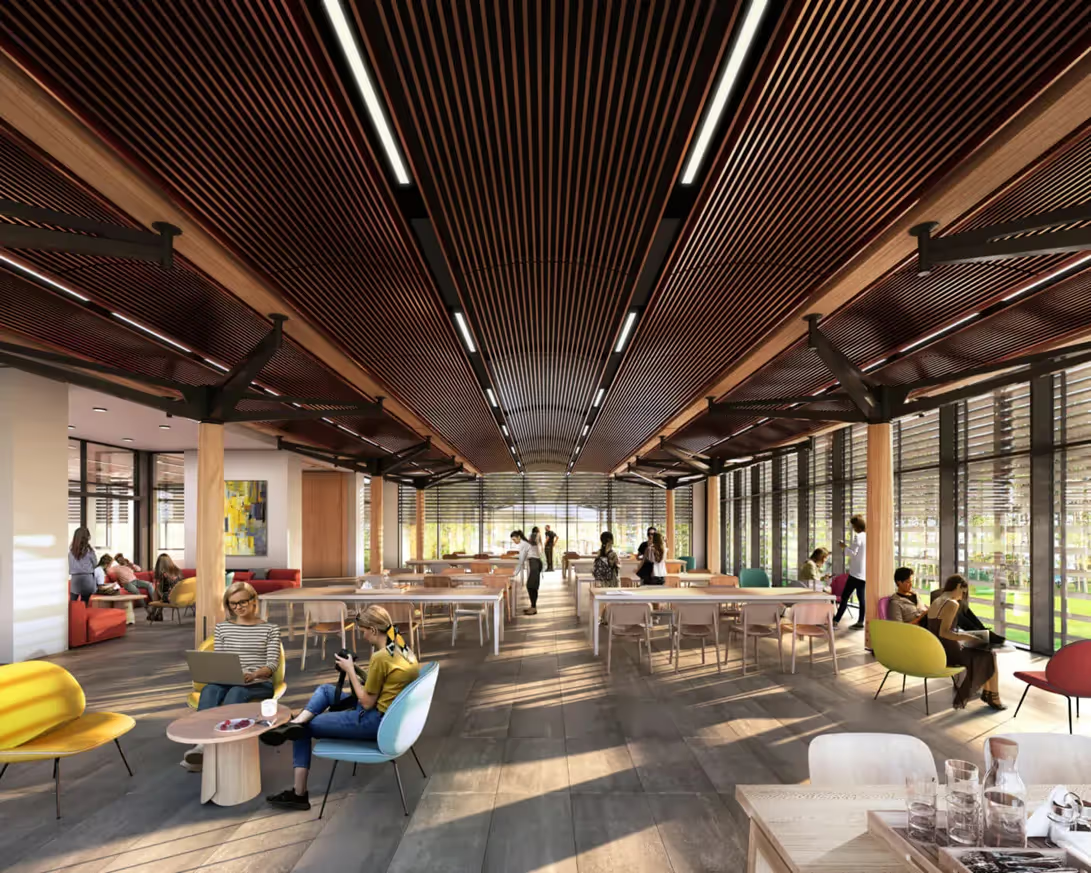
The Dining Hall includes a steel-timber hybrid design. Shaped timber columns support a CLT roof that spans between glulam beams. To create a more open plan, the architect minimized the number of columns by positioning them between the glulam beams and conceived of steel tree column capitals to cantilever and support the beams.
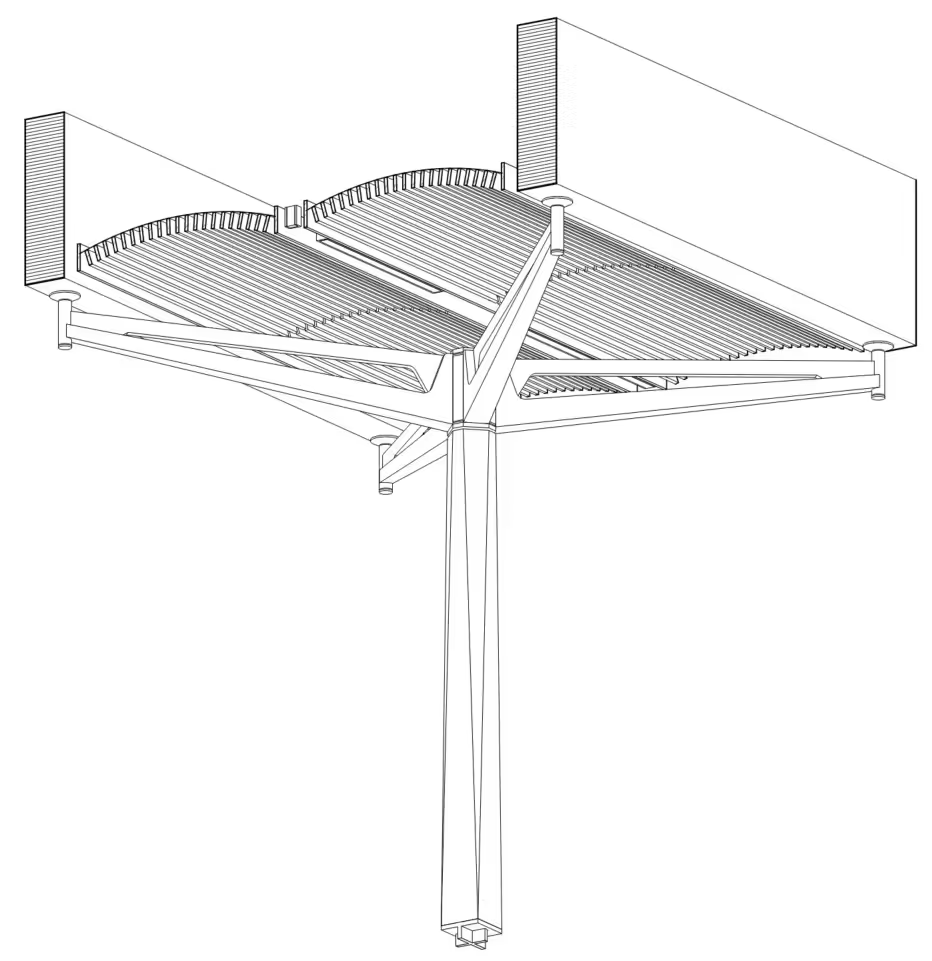
MATERIALS
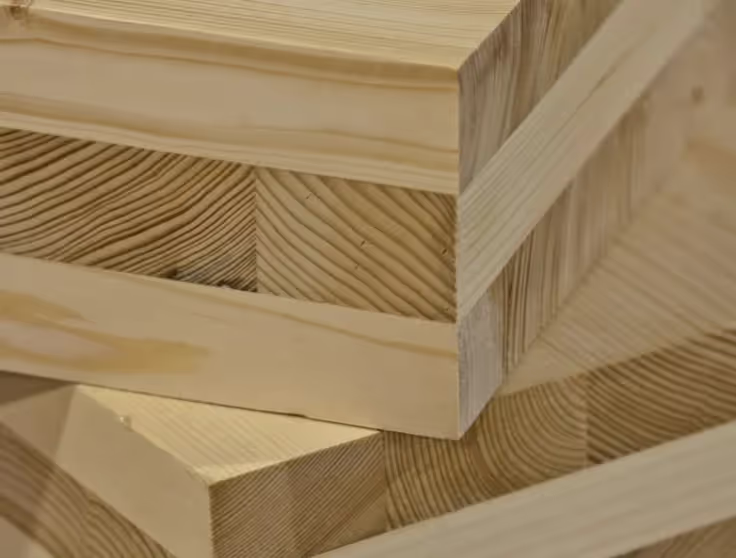
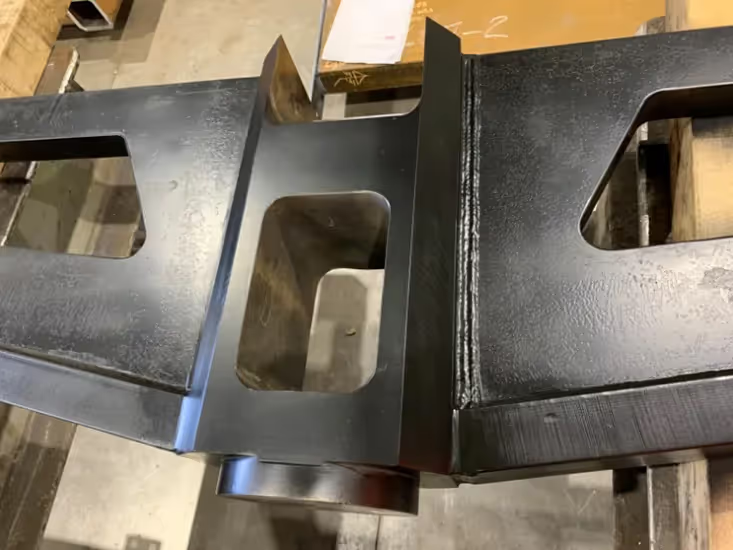
Materials for the project were carefully selected to achieve performance and sustainability targets. The inherent beauty of the mass timber structure and wood finishes offered warm, welcoming interior spaces.
Each column capital includes fabricated steel arms with custom-designed cast steel nodes. Steel was chosen for its high strength and stiffness, as well as constructability considerations. Complimenting the sustainability goals of the project, the steel castings were manufactured using electric arc furnaces (EAF) powered by a hydro-electric grid and over 95%recycled content.
WHY STEEL CASTINGS?
There are four primary reasons to consider steel castings for a project:
- Architecturally exposed structural steel connections;
- Complex geometry or loading when additional strength or stiffness is required;
- Fatigue critical connections;
- Special performance or functional requirements.
The trees were an architecturally exposed element with geometric complexity, prompting the use of steel castings.
The original architectural concept for the steel armature included a fully cast assembly, consisting of four identical cast steel arms.
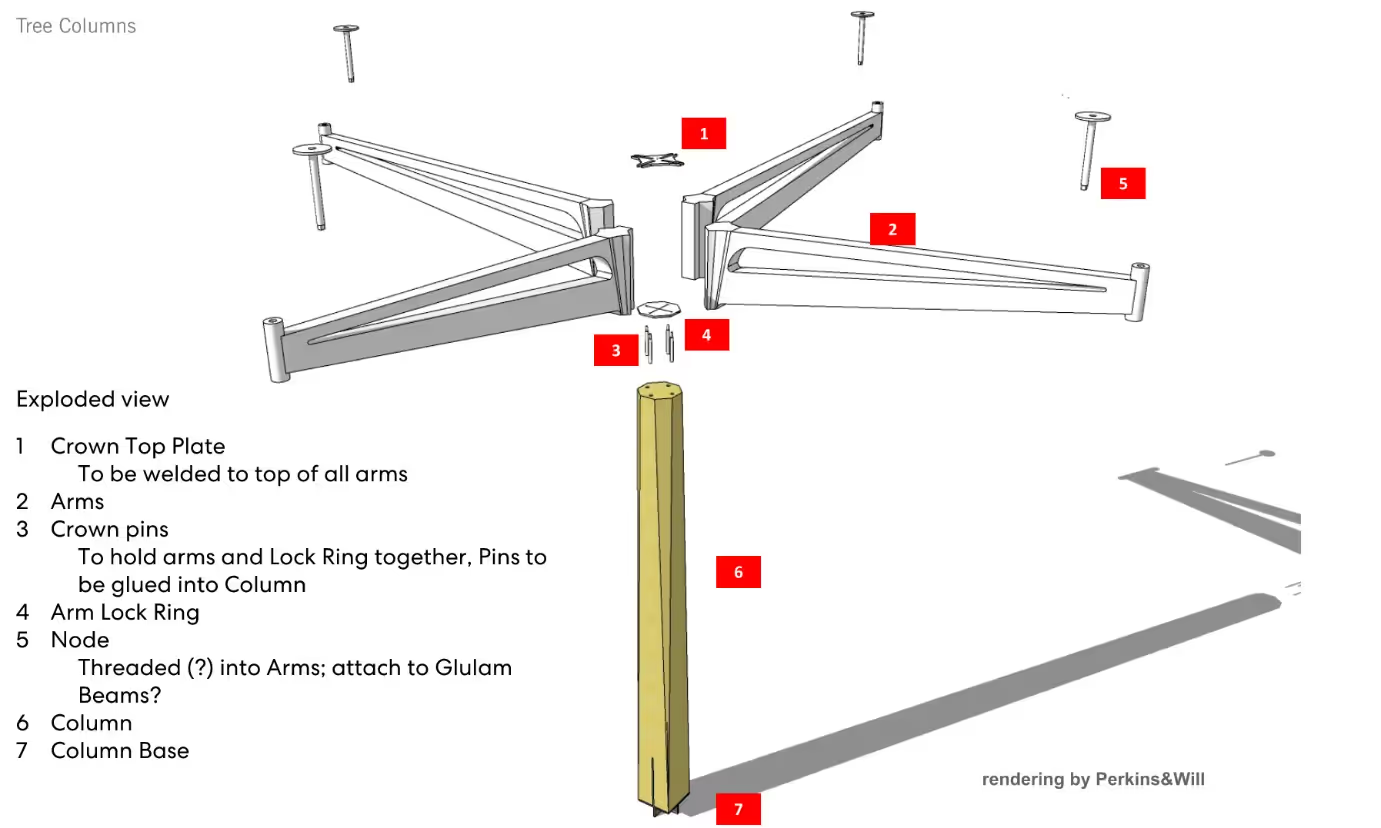
The four cast steel arms would meet at a center hub, with a top plate to tie them together. Four pins would secure the capital to the column.
CAST CONNEX reviewed the concept and through collaborative discussions uncovered the underlying challenges, which were constructability, proper fit in the field, and limits to deflection.
CAST CONNEX Custom Solution
To meet all the project goals and needs, CAST CONNEX proposed an alternate assembly consisting of two interlocking leaves. Instead of 4 independent arms assembled in the field, CAST CONNEX ideated fabricating the tree in two orthogonal “leaves”: an upper and a lower assembly. Each leaf would be fabricated in the shop, shipped flat to site, and locked together in the field.
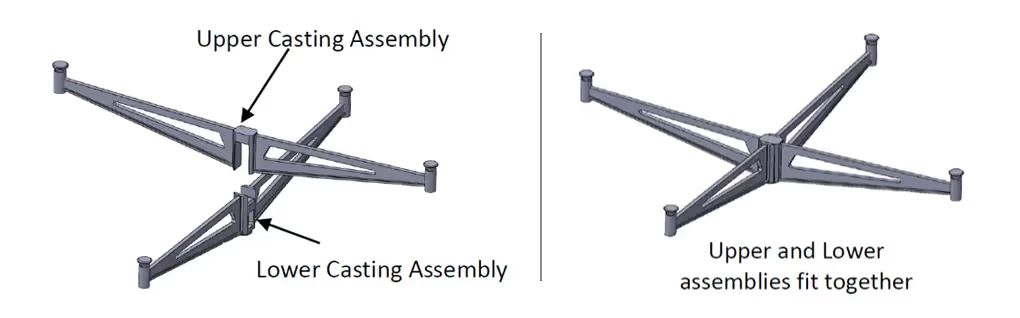
Although the original design conceived of full cast steel arms, CAST CONNEX suggested using steel castings only at the intersection where architectural quality, geometry complexity, and stresses governed. Cast steel (ASTM A958) was used to produce the interlocking central lug, while welded steel plate was used to fabricate the long arms. This provided a more economical solution, and it was ultimately more practical to build.
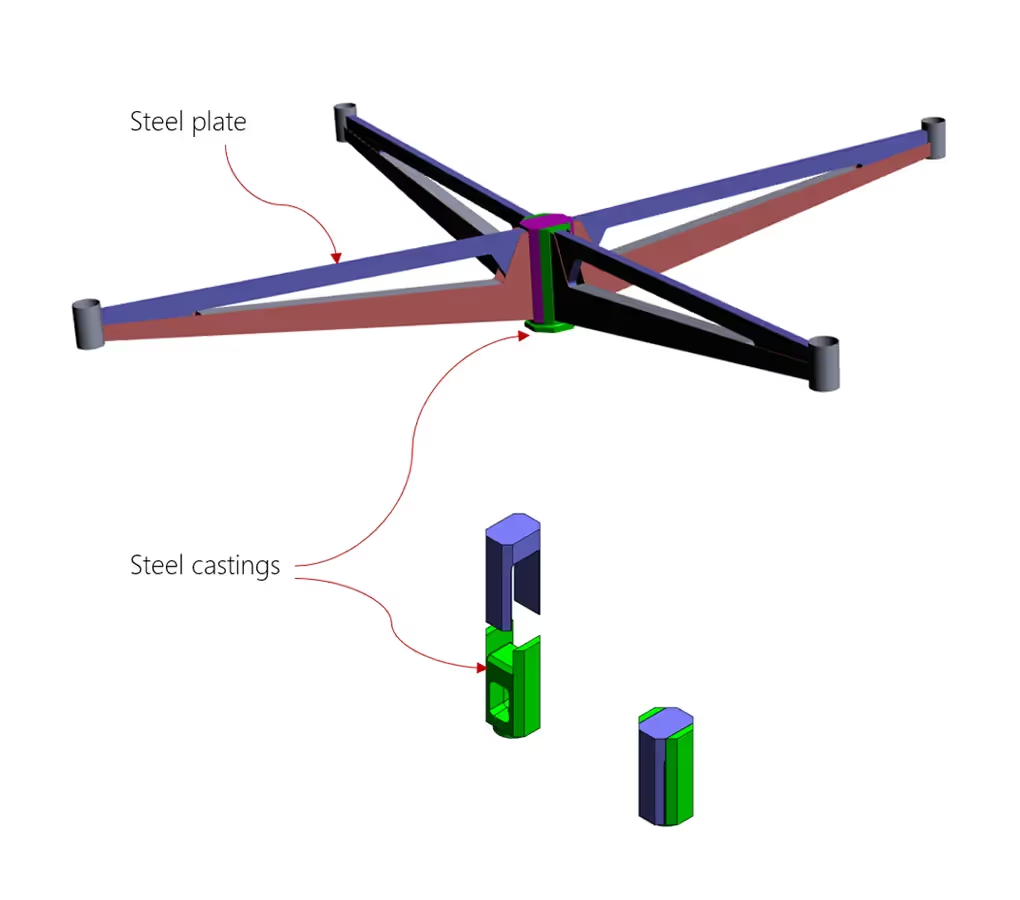
Custom Node Details
The interlocking lug included an upper and lower casting. The lower casting and assembly would be installed first and included an opening to allow access for a bolted connection to the top of column. The upper casting and assembly would be installed after, concealing this joint. This required high and precise tolerances for proper fit, which is achievable with precision-machined steel castings.
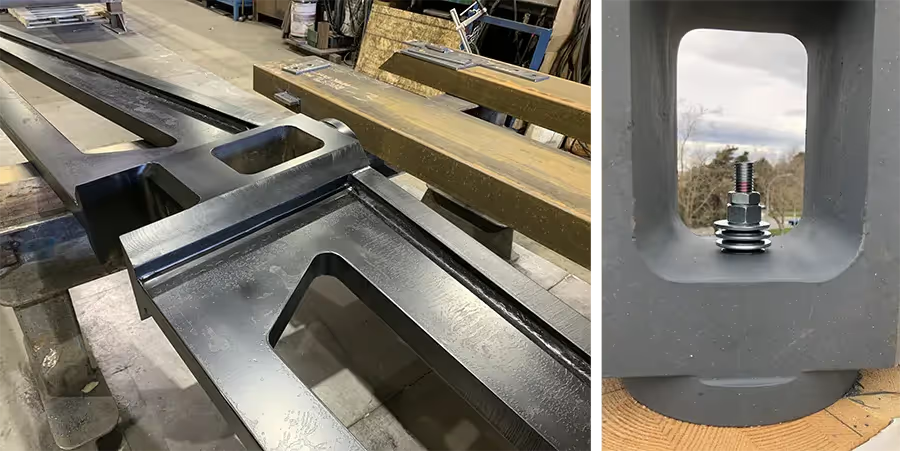
To facilitate assembly in the field, the design of the cast nodes included a small gap between the upper and lower parts. When the upper assembly lifts, the gap widens, and after installation, gravity effects close the gap. Once the gap closes, (which occurs at around half of the service load), the stiffness of the two cantilevers are virtually identical.

FEA Analysis
Individual components and the structural tree assemblies were evaluated with non-linear finite element analysis (FEA). The assembly analysis included contact elements between the components to capture any through-thickness bending effects. The models were meshed with first order tetrahedral elements, ±10-15 mm in size, while the welds were studied more closely with a ±5 mm mesh size.
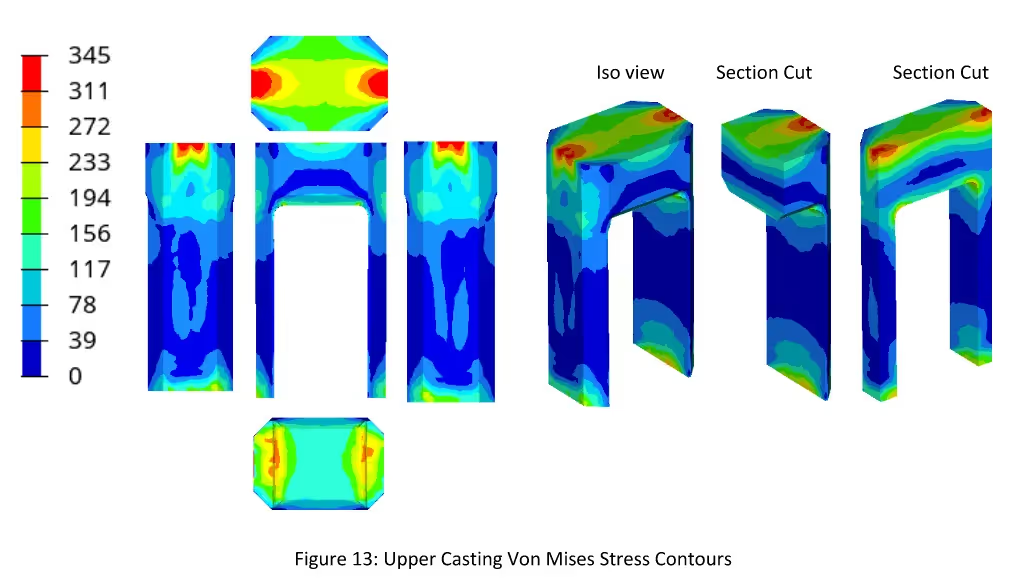
The welds between the central node halves and the arms were carefully analyzed, including the effects of shear lag.
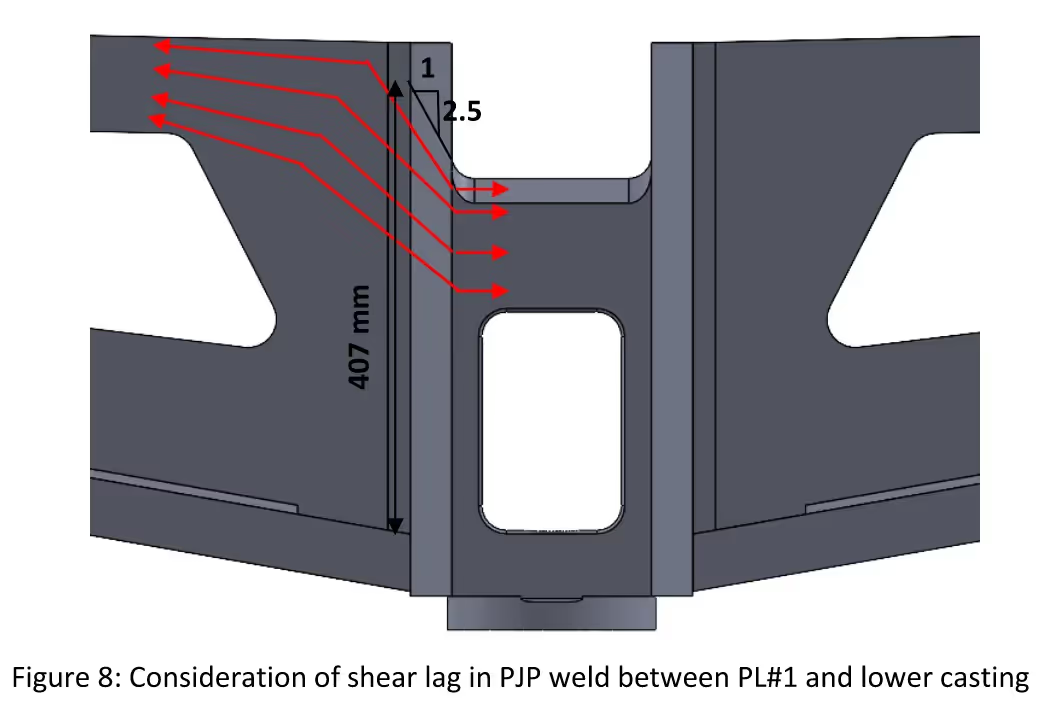
Node Inspection
First article inspection of the upper and lower castings evaluated their quality per acceptance criteria in the production specification. Quality control protocol included photometry, radiography, ultrasound and magnetic particle testing.
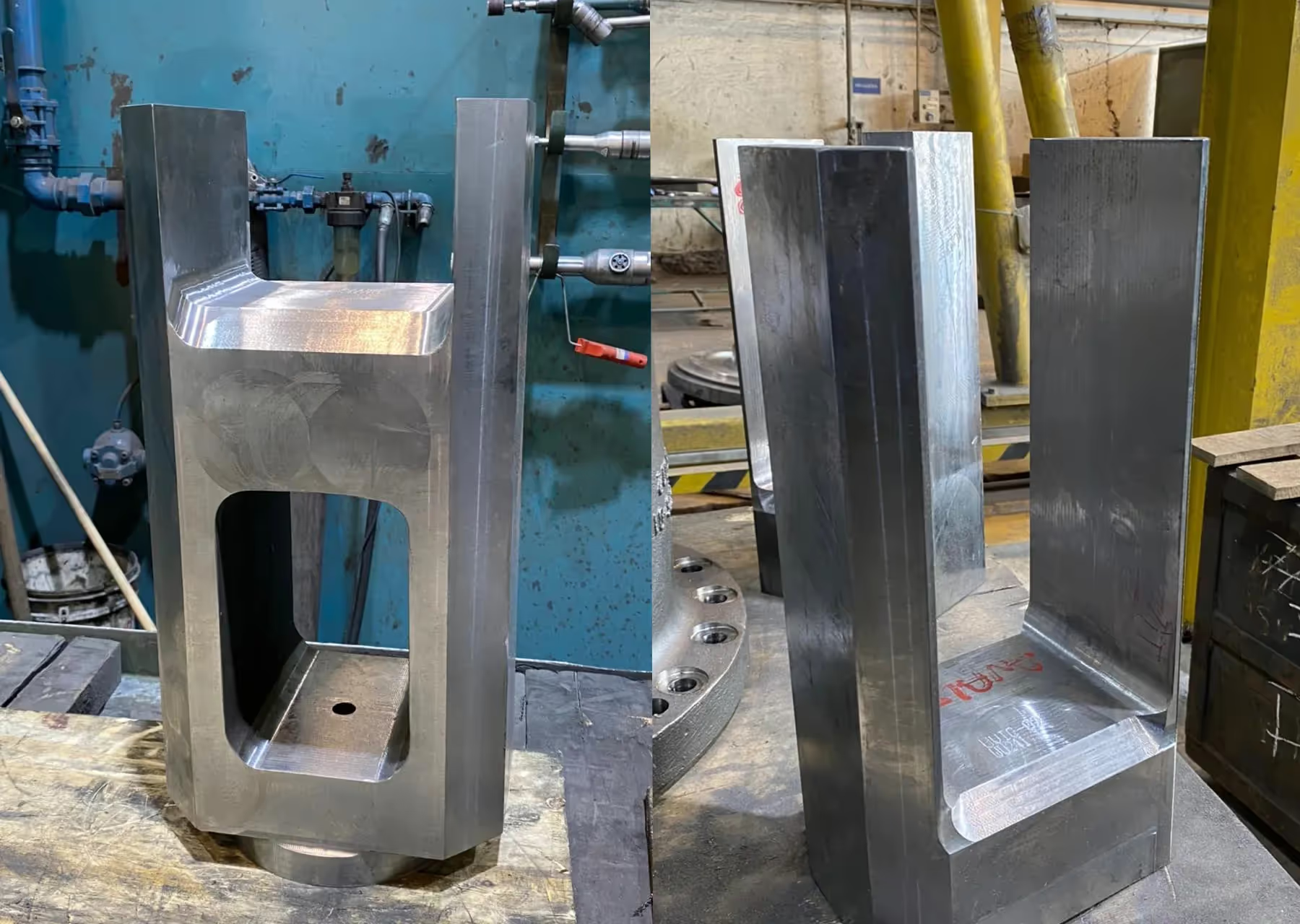
CAST CONNEX delivered the castings to George Third & Son, who completed the remaining fabrication.
PROJECT COMPLETION
Prior to delivery to the site, the assembly was mocked up in the fabricator’s shop.
The erection of the trees went smoothly. Temporary shoring in the field included struts for the timber column capital and beam seats, as the contractor installed each glulam beam.
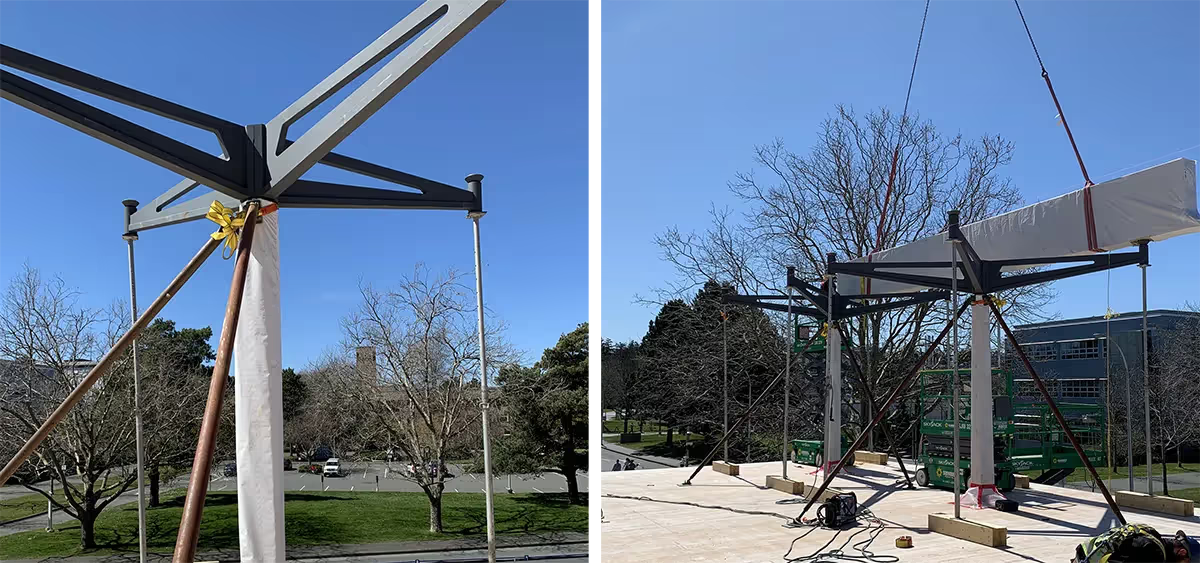
The finished project juxtaposes the warmth and softness of exposed timber with the expressive steel column capitals and bases. The material selection of cast steel nodes with timber beams and columns helped achieve the project goals for sustainability, safety, and constructability.
%20copy.webp)
Project Credits:
UNIVERSITY OF VICTORIA STUDENT HOUSING AND DINING - BUILDING 1
Owner: University of Victoria
Architect: Perkins & Will
Structural Engineer: Fast+Epp
Steel Fabricator: George Third & Son ltd.
Timber Supplier: Kalesnikoff